Our production process begins with collection of waste vegetable oil from the Sodexo Kitchens at the University of Idaho.
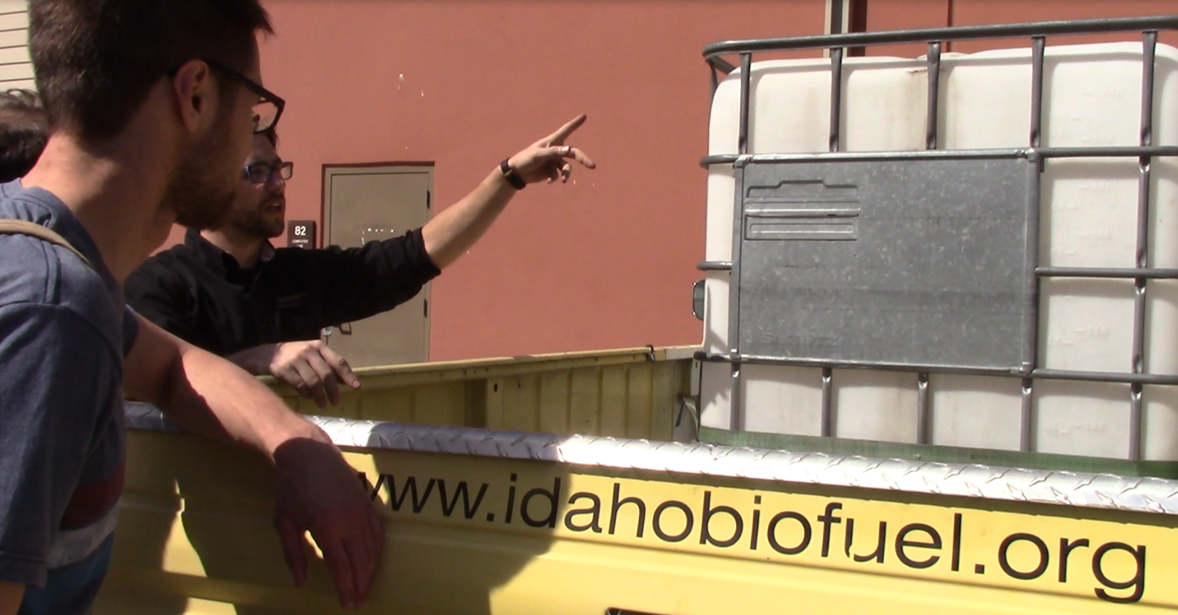
We put the waste vegetable oil in our reactor and measure the amount of free fatty acids in the oil feedstock.
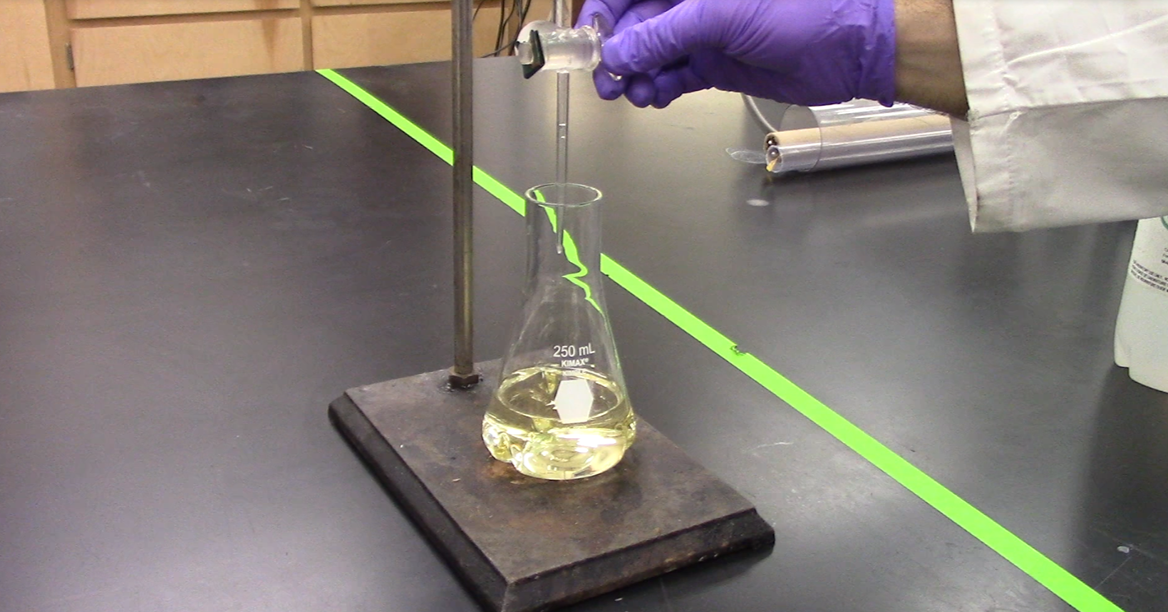
The reactor lid is closed and the temperature of the oil in the reactor is below 65°C. The methanol condenser vent tube is installed and turned on.
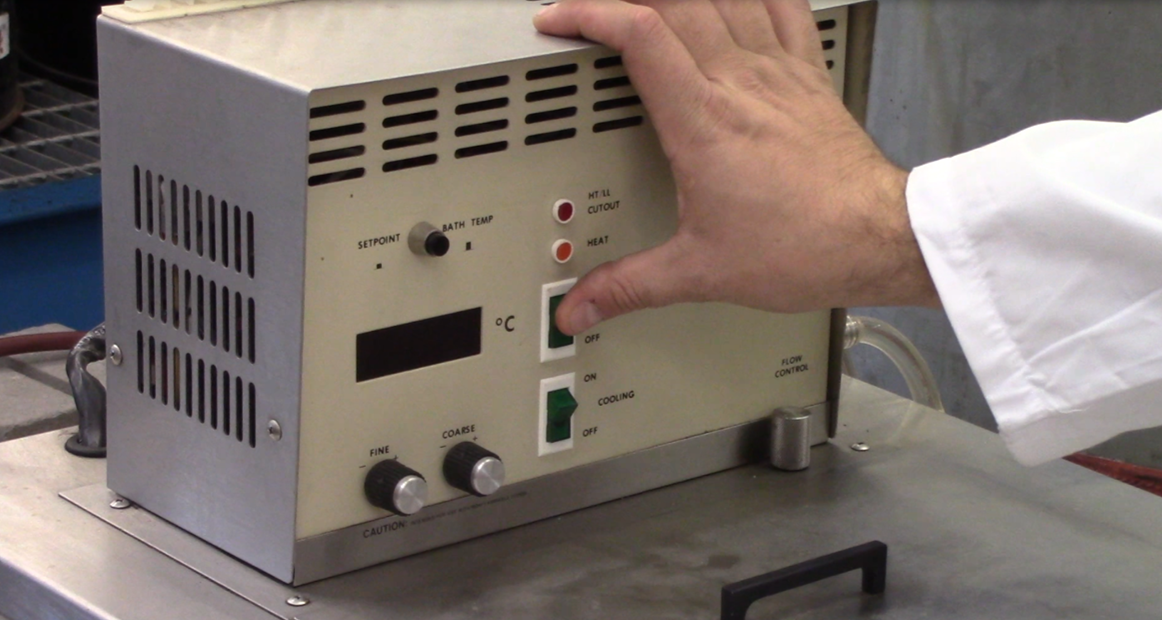
80% of the methanol used in our calculation is pumped into the reactor below the surface of the oil.

Using the value derived from the calculation, 80% of the catalyst solution is added to the reactor.
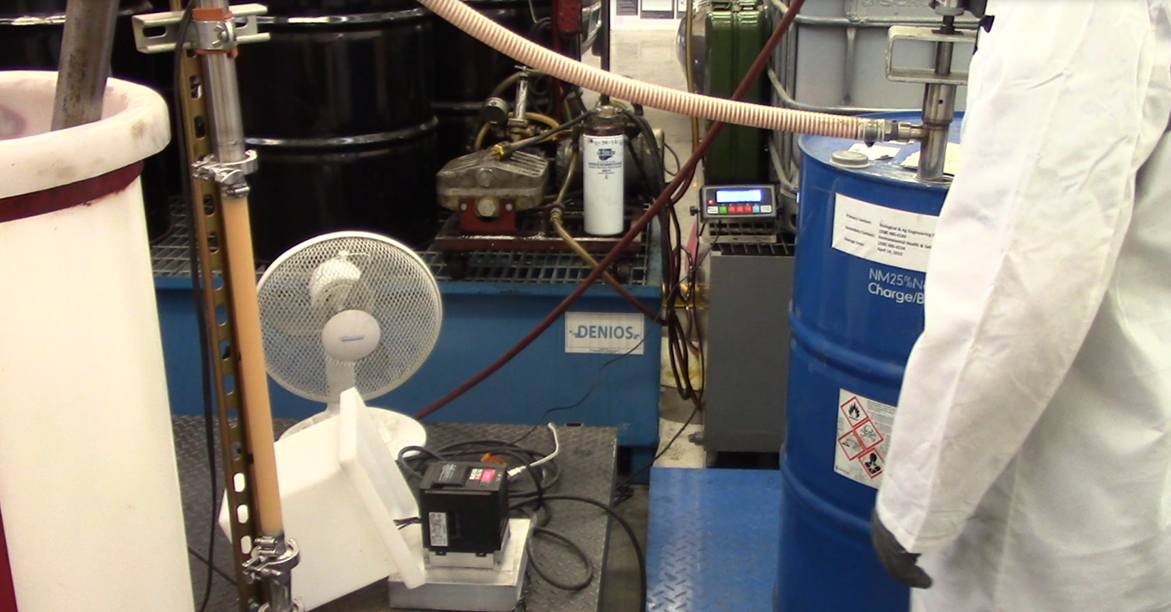
The reactor is maintained at 55-60°C and the reaction mixture is mixed vigorously for at least one (1) hour for the first reaction.
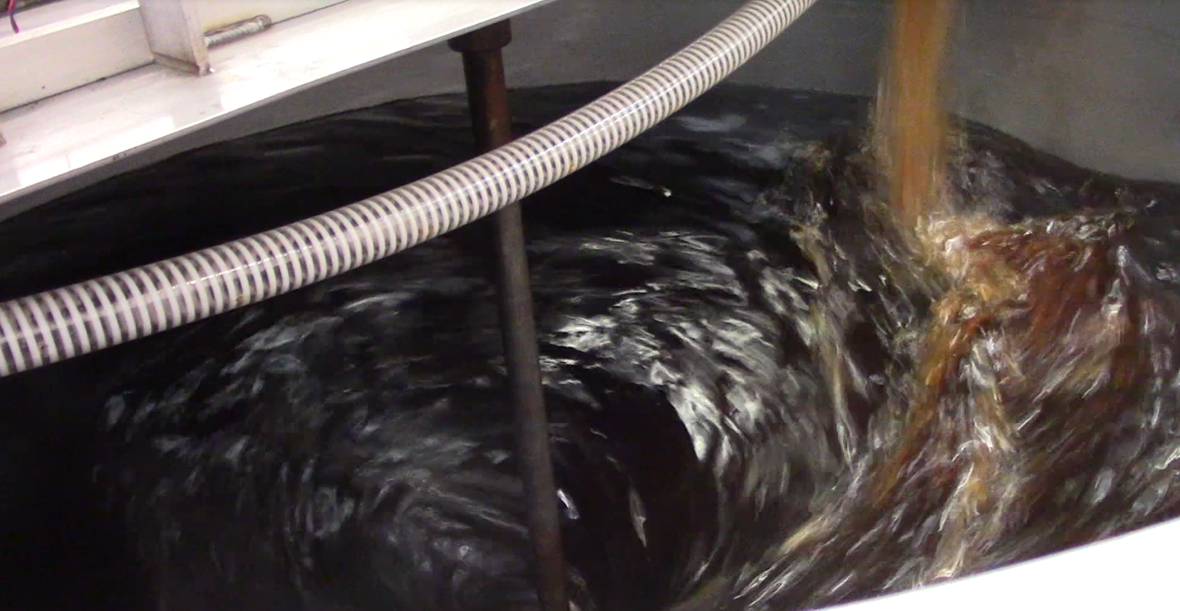
After the first reaction, the agitation is turned off to allow the phase separation of biodiesel and glycerol for at least two (2) hours before the glycerol is removed.

The remaining 20% of the alcohol and of the catalyst solution are then added using the same method described above.
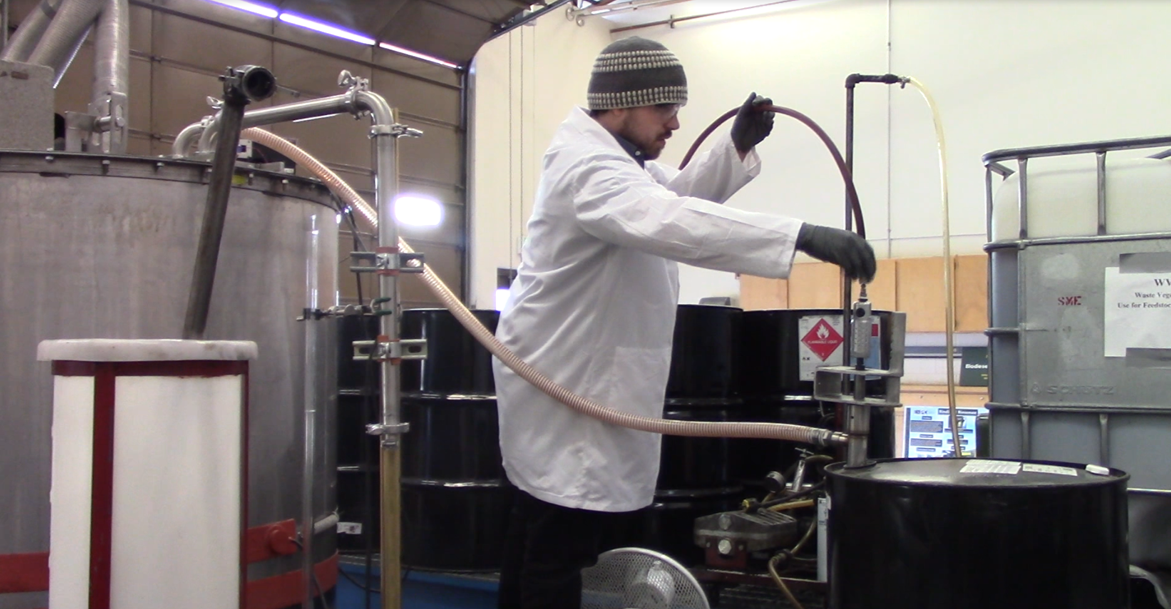
Water washing is done by turning off the heat to the reactor and pumping water at one-quarter (¼) of the amount of fuel through the perforated tube above the surface of the biodiesel under gentle mixing.
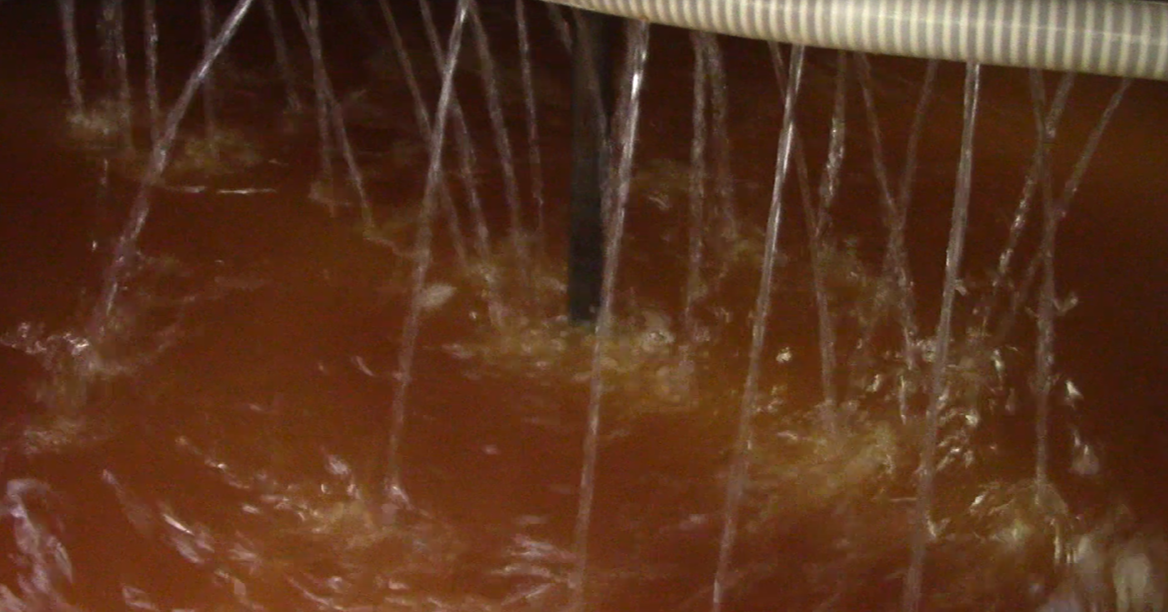
This process of raining water under gentle agitation, separation and draining are repeated until the soap content is below 5 ppm. Once the soap is below 5 ppm, the mixer is then turned off to allow separation of grey water and the grey water is removed.
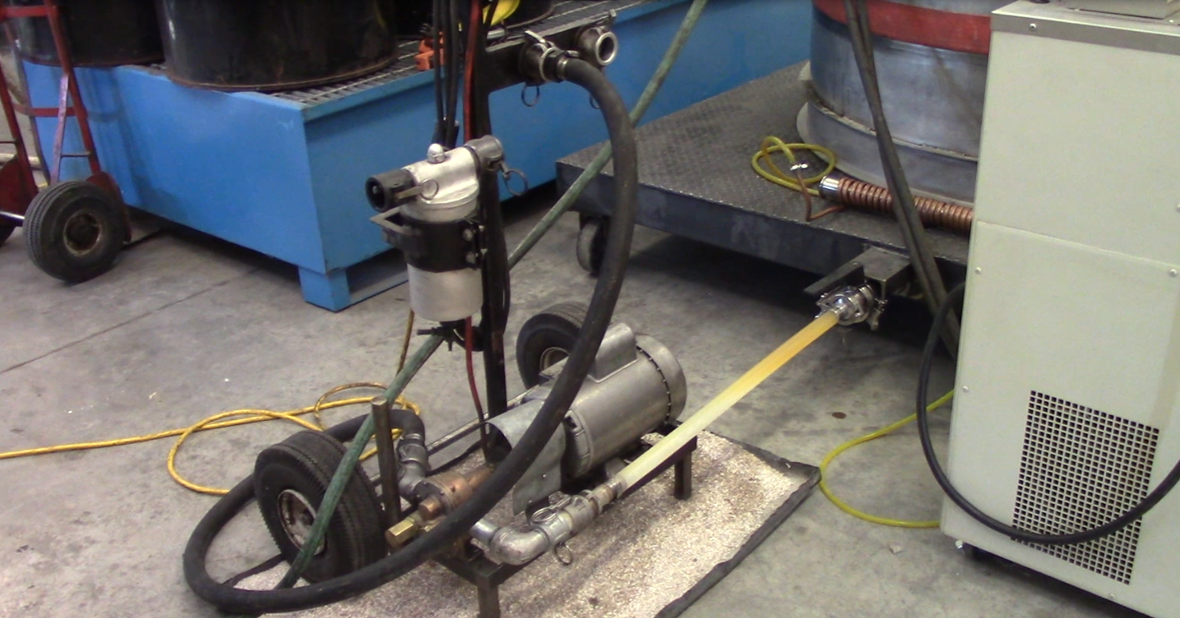
The biodiesel is dried until the water level is below 500 ppm.
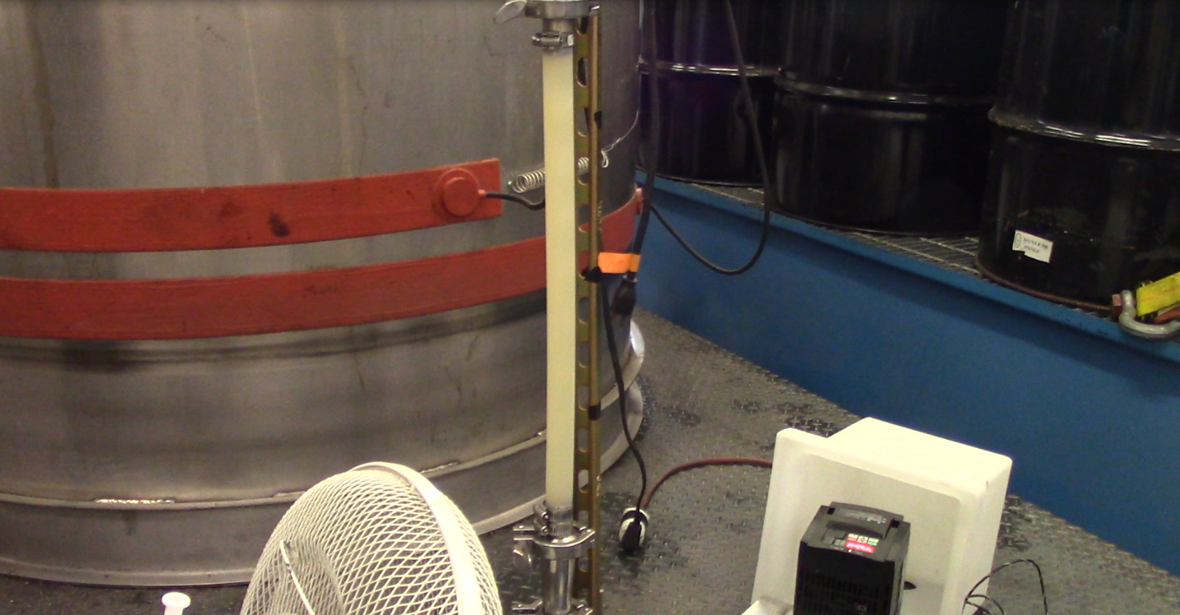
An antioxidant is added at a dose of 200 ppm and the oxidative stability is measured. If this amount of additive does not result in an oxidative stability reading of 3 hours or more, an additional 200 ppm will be added and the fuel retested.
A series of tests are made on the finished product to certify it meets the ASTM biodiesel standards. If the fuel fails any test, attempts will be made to rectify the situation.
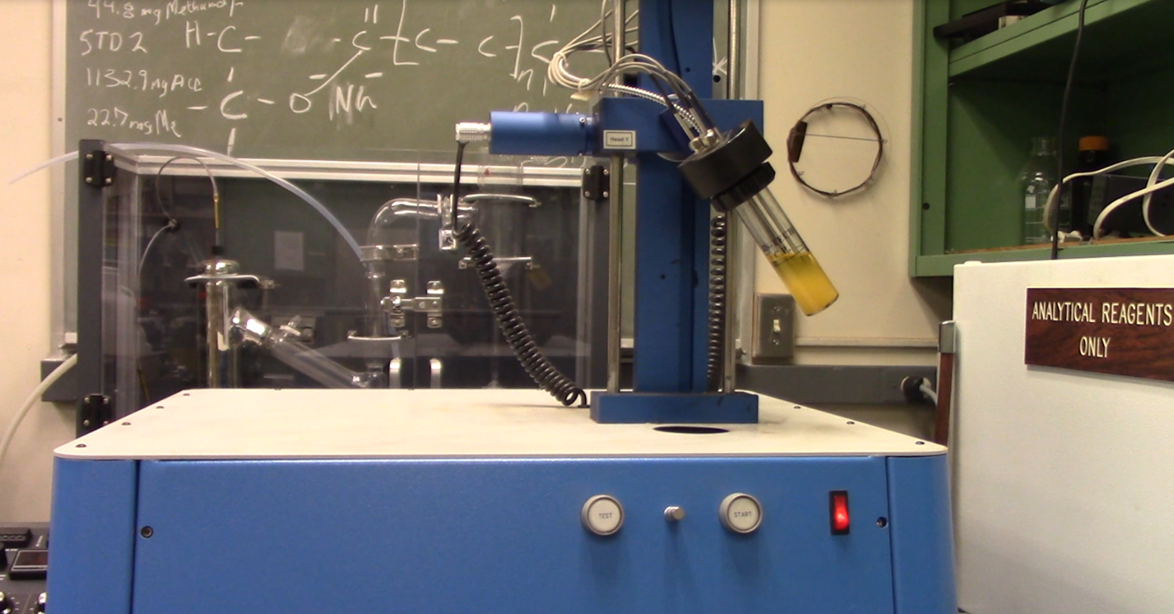
Once the fuel has been shown to meet the standards, a biocide additive is added to the fuel at a dosage prescribed by the maker.
The finished biodiesel is allowed to cool down to a minimum of 30°C, then pumped into clean and dry storage containers. Full storage containers are sealed and labeled.
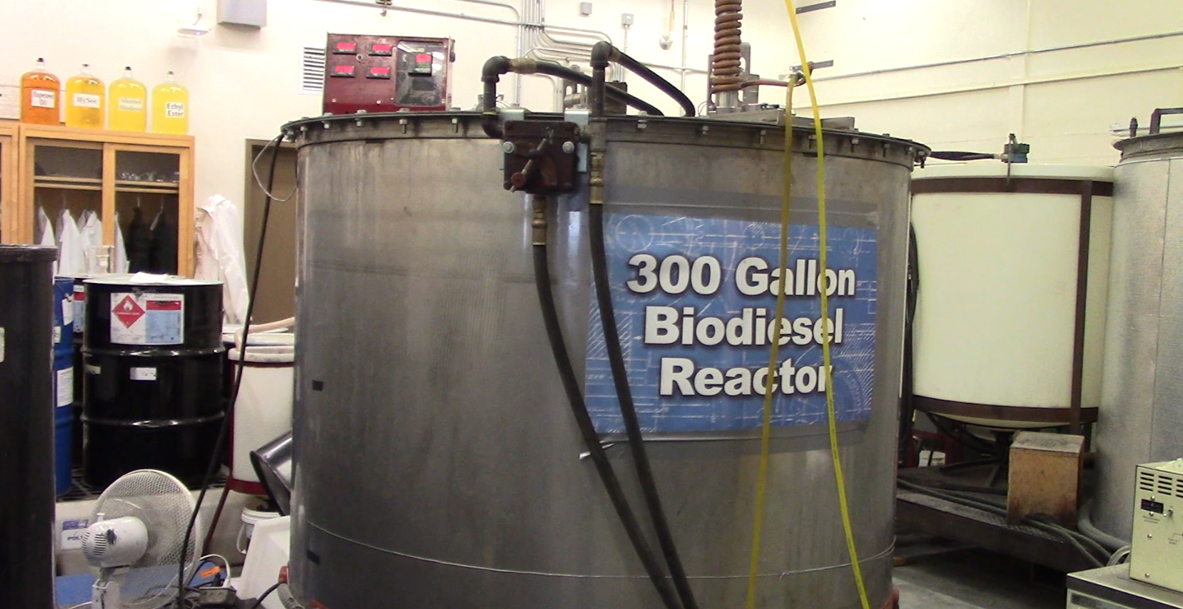